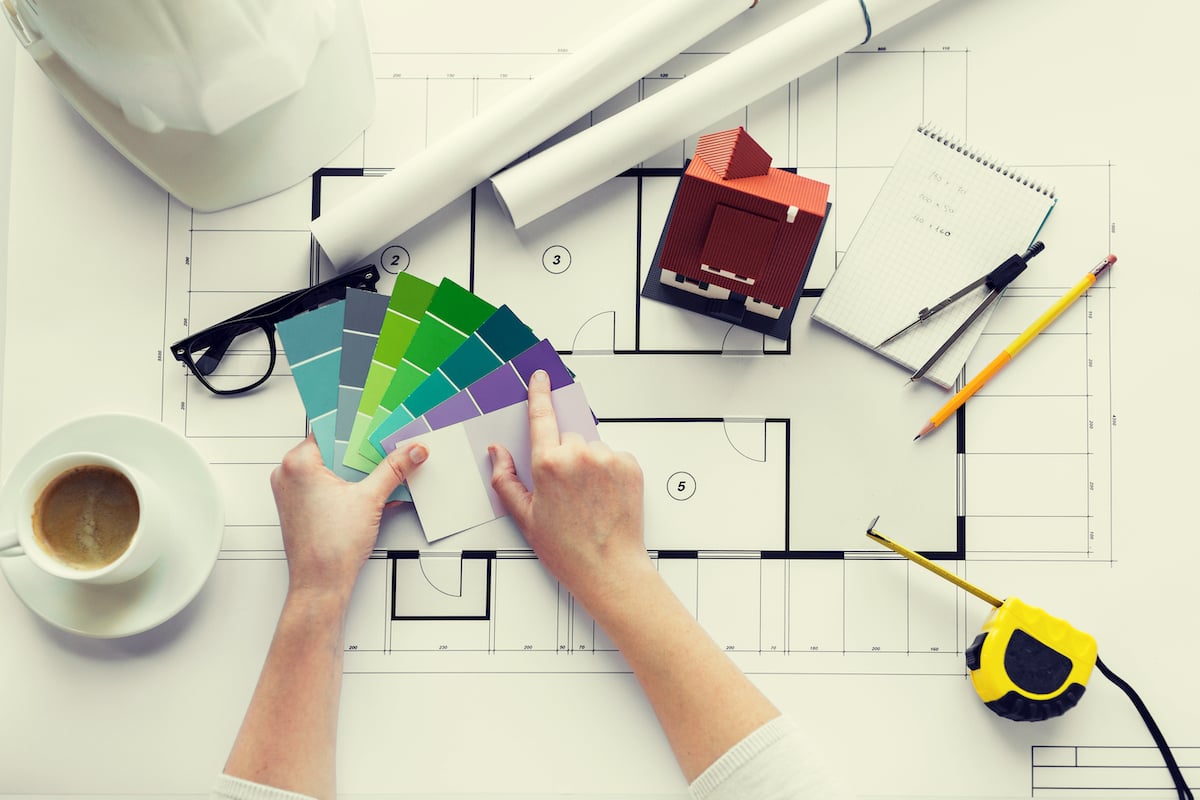
In the heart of the pandemic-driven lockdown, while many companies were struggling to survive, one industry skyrocketed: the cleaning industry. In November 2020, Clorox reported its best quarterly sales in more than two decades, and its stock price soared 36 percent over the year. Everyone wanted to make sure their homes were sanitized, and what better way to do that than with bleach?
But this logic doesn’t transition so seamlessly to the interiors industry. In fact, most interiors surfaces, excluding perhaps those made for the healthcare environment, are not bleach cleanable. And yet, as the vaccine rollout gives rise to conversations about return-to-office protocols, many are realizing that more settings outside of hospitals need surfaces that can be deep cleaned. So, what are people looking for, and how can specifiers be prepared to address some of the biggest concerns of a post-pandemic world, one that undoubtedly will be more conscious of germs for the foreseeable future? We sat down with Walter Marin, founder and senior principal of NYC-based Marin Architects, to understand his firm’s view of antiviral protocols and paired his insights with ThinkLab research to provide a glimpse into how design can aid in overall health and safety for the interiors industry.
What is the demand?
Let’s start by gauging just how big the demand for this antiviral market will be. For starters, when polled in a Fall 2020 ThinkLab research study, 62 percent of specifiers believed that COVID-19 had either increased or greatly increased the need for bleach cleanable materials, while 55 percent felt the same about antimicrobial materials, and 48 percent thought so about antiviral materials.
Much of the debate centers on cleaning versus sanitizing. Prior to COVID-19, surfaces generally came with instructions on how to clean them. But not all came with details on how to sanitize them. According to the CDC, “cleaning removes germs, dirt, and impurities from surfaces or objects” and “disinfecting kills germs on surfaces or objects.” Meanwhile, “sanitizing lowers the number of germs on surfaces or objects to a safe level, as judged by public health standards or requirements.”
Simply put, in the short term, the focus is on making people safe. However, the extent of long-term change to materiality due to COVID-19’s impact is still uncertain. Using healthcare-level cleaners may lead to product failures and warranty claims, and most informed designers are not putting their support behind antiviral or antimicrobial materials because their concern for sustainability issues is greater.
So what’s the logical next step?
Perhaps because of this uncertainty, Marin suggests that some specifiers are looking for materials that naturally repel bacteria and germs by design. While copper and wood have long been known for their ability to kill bacteria and viruses, Marin shares that specific textures are equally important in material selection. He explains, “Many designers are following the science behind shark skin to select textured materials that naturally reduce bacteria. Sharks tend to travel in areas that are not as clean as other fish, and therefore their skin is textured like roof tiles. The nature of this texture minimizes the surface area and does not allow bacteria to survive. In the construction industry, there is an awareness that mold loves nice flat surfaces, like drywall or sheetrock. There was a huge industry that grew out of this concept, that surfaces should have a texture to avoid bacteria. Now in light of COVID-19, everyone is thinking about this.”
He continues to explain how textures and germs will be a common consideration factor for non-medical specification moving forward. “Everything we look at, touch or walk through someone picked. There is an enormous number of things we need to talk about. For example, our industry used to specify spackled ceiling tiles, but it was not long before we realized that they attract dust easily. We no longer specify those. In the long run, I believe there will be a lot more thought put into how a material behaves and how it can be cleaned and disinfected in the future.”
Another route that designers are beginning to explore is how to minimize high-touch surface areas altogether. Marin explains, “Touchless doorways have been present at hospitals for many years. Now, we are seeing other industries incorporate sensors, motion-activated lights, and automated doors. These mechanisms not only protect surfaces from germs but are also beneficial for elderly and disabled people.”
And what about air?
And while surfaces were a big consideration point at the beginning of the pandemic, Marin reminds us that, for the immediate future, we need to consider one of the most prominent ways this virus spreads – through the air. He adds, “As architects outside of the healthcare industry, we are not accustomed to thinking about how our designs will protect users against air particles that threaten our health. In order to address this new concern, we must start to think about how the strategies we use in the design of healthcare facilities can be applied to other markets, from office buildings to senior housing to residential buildings, and beyond.”
He continues, “One of the biggest considerations we focus on when designing medical buildings is air circulation. When you are walking through a hospital, you will notice that it is very hard to detect any smells, due to the advanced rate at which air is being filtered in and out of the building. In the long term, we will see more systems like this being utilized in market sectors beyond the healthcare industry. It is, however, quite an expensive solution, which is why in the short term, many are choosing to install secondary air cleaning devices, which are not quite as impactful.”
Marin suggests that the traditional construction cycle can take as long as three years, so he suggests that installing enhanced air filters (as opposed to a brand-new filtration system) is the biggest asset designers can implement right now without doing a major redesign.
As for the future, Marin leaves us with this, “The entire world knows that there is this new virus and there are all these rumors about what it can and cannot do. I think at the end of the day, what we, as a design industry, have learned, is that attention to detail in material selection is such an important part of the health and safety of a space. It’s our time to shine, and by mindfully selecting the right properties of a material, and pairing it with expertise in systems and filtration selections, we can be an advocate for our clients and help them design safe spaces for their end users.”
Amanda Schneider is President of ThinkLab, the research division of SANDOW. At ThinkLab, we combine SANDOW Media’s incredible reach to the architecture and design community through brands like Interior Design Media, Metropolis, Luxe, and Material Bank with proven market research techniques to uncover relevant trends and opportunities for the design industry. Join in to explore what’s next at thinklab.design/join-in.